Quality
We operate in a pharmaceutical environment and are therefore obliged – together with our customers and suppliers – to meet high quality standards.
Product quality, patient safety, and data integrity – these are the high values in our industry which serve as a basis for the high level of quality we strive to achieve in our daily work.
The constant controllability of the entire supply chain and the reliability of our daily work are governed by a variety of regulatory guidelines and laws.
Quality Management
Our quality management system is based on the German Drug Law [AMG], the German Ordinance on the Production of Pharmaceuticals and Active Substances [AMWHV], the Ordinance on Trade with Medicinal Products [AM-HandelsV], the EU GMP guidelines and the EU GDP guidelines in their current valid versions.
All of our work processes are SOP-controlled, our installations and equipment are qualified and our inventory control system is validated.
All of the relevant functions under pharmaceutical law are competently filled and competent stand-in arrangements are in place.
- Qualified person / competent person
- Quality assurance
- Quality control
- Person responsible for narcotics
- Information Officer
- Pharmacovigilance Officer
- Head of Production
The Executive Board is actively involved in quality management.
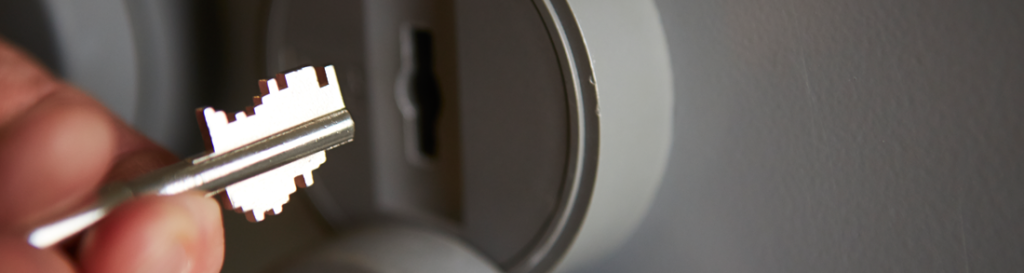
GMP Conformity
Naturally, all manufacturing processes are regulated by corresponding manufacturing instructions, manufacturing protocols and in-process controls. All materials are recognized in the balance sheet.
The entire process is audited by the qualified person. This forms the basis for the issue of the Certificate of Conformity and approval.
The manufacturing process comprises the marking, labelling, packaging and repackaging of pharmaceuticals and materials for clinical trials.
GDP Conformity
In our company, all logistic processes along the entire supply chain are SOP-controlled and executed in a GDP-conform manner.
All pharmaceuticals are batch-managed and shown in our inventory control system.
FEFO warehouse management is used predominantly. Only non-pharmaceuticals such as advertising materials are entered according to FIFO. Other warehousing strategies are possible in line with specific customer requirements.
Compliance Programme
Our industry operates in a complex, difficult and very responsible environment. Incidents of counterfeit drugs and other criminal activities are common the world over.
In line with our philosophy of transparency, responsibility and openness, we have imposed a compliance programme incl. an anti-corruption concept which precisely corresponds with our sincere and responsible approach.
Air-conditioning
Our warehousing and manufacturing areas are equipped with state-of-the-art air-conditioning.
We operate warehouses in a temperature range of +15 to +25 °C for ambient articles and +2 to +8 °C for articles that must be refrigerated. The warning limits are each set at an increment of 1 °C, i.e. at +16 °C and +24 °C or +3 °C and +7 °C so that we can immediately respond in the event of a temperature deviation.
The consistency of the temperature control in the warehouses is controlled by textile air outlets on the ceiling of the warehouse to prevent the extreme formation of cold spots and hot spots and guarantee consistent temperatures of +15 to +25 °C for ambient articles +2 to +8 °C for articles that need to be refrigerated.
Hygiene
Our material and personnel flow concepts also incorporate inlet and outlet processes, particularly within the framework of the manufacturing processes.
Cleaning schedules are implemented in all GMP and GDP-relevant rooms as a matter of course.
Rentokil is our chosen service provider for monitoring and preventative measures against rodents and flying insects and customers can therefore rest assured that their goods are in a safe warehousing environment.
Personnel
All of our employees are educated and trained specifically for their respective activities. Annual training programmes ensure that all employees are always up to date.
External and internal training guarantees that our employees are always abreast of the latest developments.
We are appropriately staffed to cover all of the relevant functions under pharmaceutical law and are therefore in a position to handle all important warehousing, order-picking, manufacturing and labelling activities. Our personnel resources include:
- Qualified person / responsible person
- Quality assurance
- Quality control
- Person responsible for narcotics
- Information officer
- QPPV – Qualified Person Pharmacovigilance
- Head of Production